Incidents & Fines in the Manufacturing Industry
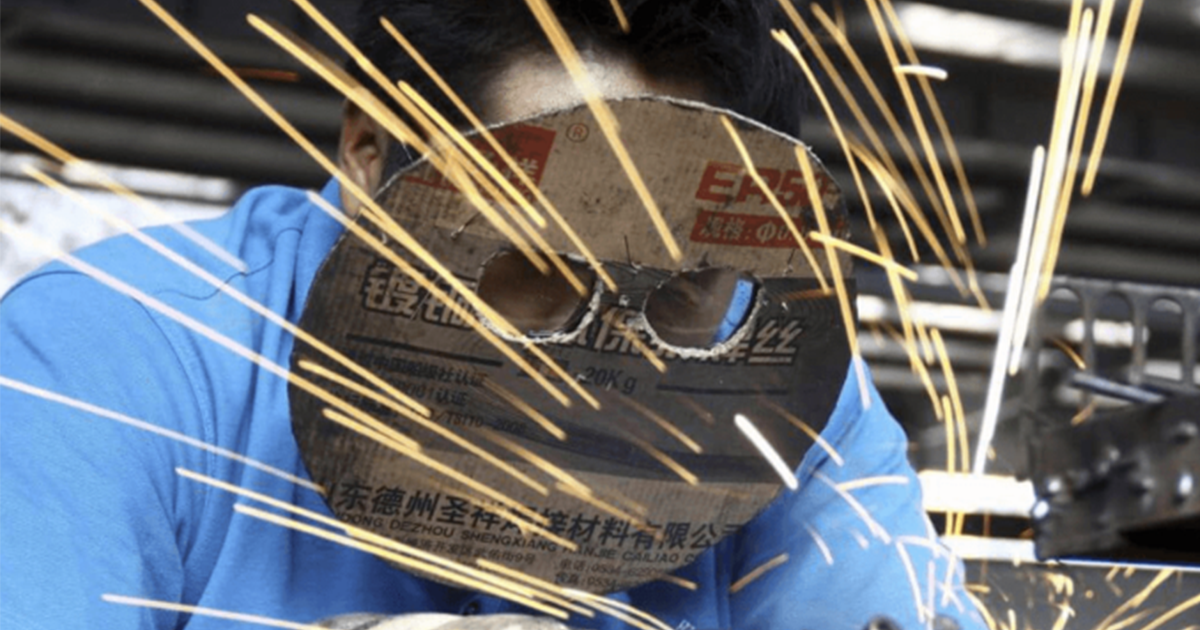
Are you struggling to get your board approval to adopt an incident reporting software ? This article may help getting their
approval above the line…
Although manufacturing has lower accident rates than construction and agriculture (measured per 100,000 employees) the industry still accounts for a significant proportion of accidents at work.
CHAPTER 1
Accidents In The Industry
The industry was responsible for 27 deaths of UK workers in 2015/16. Whilst there were around 12,500 reported non-fatal injuries (those where someone is off work for more than seven days or is treated in hospital, or both) the Labour Force Survey estimates that there were about another 50,000 non‑reported accidents.
Fatalities are classified by the HSE by type, and most common amongst the fatalities over the last five years have been: ‘struck by an object’, ‘contact with machinery’, ‘fall from a height’, and ‘trapped by something collapsing’.
Traditional manufacturing injuries can be typified by the incident that leads to a recent £400,000 fine for the shipbuilder, Cammell Laird. There was a written safety management system, which described a process of lock-off to be used by maintenance staff when repairing, adjusting, or cleaning lathes. However, practice had been for machinists to carry out their maintenance and cleaning. In this case, the worker’s hand was pulled into the machine whilst he was cleaning it.
CHAPTER 2
Illnesses and Disorders
The Labour Force Survey also highlights problems with ill-health caused by work and reported that each year, around 80,000 manufacturing workers in GB suffer from an illness they believe was caused or made worse by their work. Musculoskeletal disorders (MSD) account for nearly half of this ill-health, and exposure to vibration causes a further significant proportion of illnesses.
The use of vibrating tools is known to cause irreversible damage to hands, in extreme cases leading to disablement. Hand-Arm Vibration Syndrome (HAVS) includes two specific conditions – Vibration White Finger (VWF) where the fingers turn white because of repeated damage to nerves and blood vessels and Carpal Tunnel Syndrome (CTS) where the nerve is compressed at the wrist, leading to tingling, numbness, and pain in the whole hand.
The controls for HAVS are very straightforward and include eliminating hand-held vibration tools, reducing time spent using such tools, and providing health surveillance for at-risk workers.
CHAPTER 3
Fines From Regulators
Interesting to see therefore that the regulator is pursuing manufacturers who fail to protect workers against HAVS and MSD. Asset International Ltd manufactures sewage pipes. In 2011 a worker who frequently used a vibrating power saw to cut through the pipes complained to his manager about tingling and numbness in his hands. His manager did nothing, and although his doctor warned him of the long-term effects, he carried on working. Two years later, he couldn’t stand it any longer and complained again. A better-informed manager immediately told him to stop working with vibration tools, and investigated the problem more broadly, discovering seven more cases of VWF and CTS.
Asset International was fined £200,000 for failing to follow the Control of Vibration at Work Regulations, with the fine reduced because of the enormous efforts made since discovering the problem, which they had voluntarily reported under RIDDOR.
Asset International spent nearly £1 million to replace many of the tools with new equipment, implemented a maintenance regime for tools, improved their risk assessments, enhanced their health surveillance programme to include HAVS, and retrained staff so that they can use better job rotations to reduce exposure.
CHAPTER 4
HSE Inspections
When the HSE received six reports within 14 months of workers from the same Northampton factory taking more than seven days off work due to back injuries, it decided to investigate. Investigators found many more workers suffering from back problems, but working through the pain or taking shorter periods of leave. Work on the production line involved lifting engine parts weighing up to 21kg “hundreds of times” during a single shift.
Mahle Powertrain had no relevant risk assessments and no suitable handling aids. In other factories, similar operations had already been automated, and Mahle has since spent £700,000 upgrading the equipment to reduce the element of manual handling. Nevertheless, the original offence resulted in fines and costs of £200,000 for breaching the Manual Handling Operations Regulations.
For more information as to how EcoOnline is used by customers in the manufacturing sector to improve their health and safety management procedures, you can Request A Demo or contact us for more information.